Drilling Program
In mid 2023, the Company commenced a new 4,100 m drilling program to retrieve fresh samples at depths of up to 420 m from the slope areas for both the planned mining pits at Valencia and Namibplaas.
The drilling program focuses on:
• Geotechnical logging and geo-mechanical sampling to refine pit designs;
• Sampling for new metallurgical test work and for optimized process design;
• Sampling and testing local groundwater resources and to establish additional groundwater monitoring borehole;
• Further geotechnical drilling, logging and sampling, along with downhole surveys (trajectory, gamma, Optical Televiewer) at Valencia and Namibplaas;
• Density test work on ore and waste material;
• geochemical analysis of samples at Trace Element Analytical Laboratories and calc index and U deportment test work; minimum of 5% check analyses by other independent analytical laboratories.
Figure-1 below, illustrates the drilling program within ML-149 Valencia and EPL-3638 Namibplaas (ML-251 pending). Currently one Reverse Circulation (“RC”) drill rig and two Diamond Core (“DC”) drill rigs are on ML-149. Additional drill locations are planned for further in-depth studies and for geotechnical assessments.
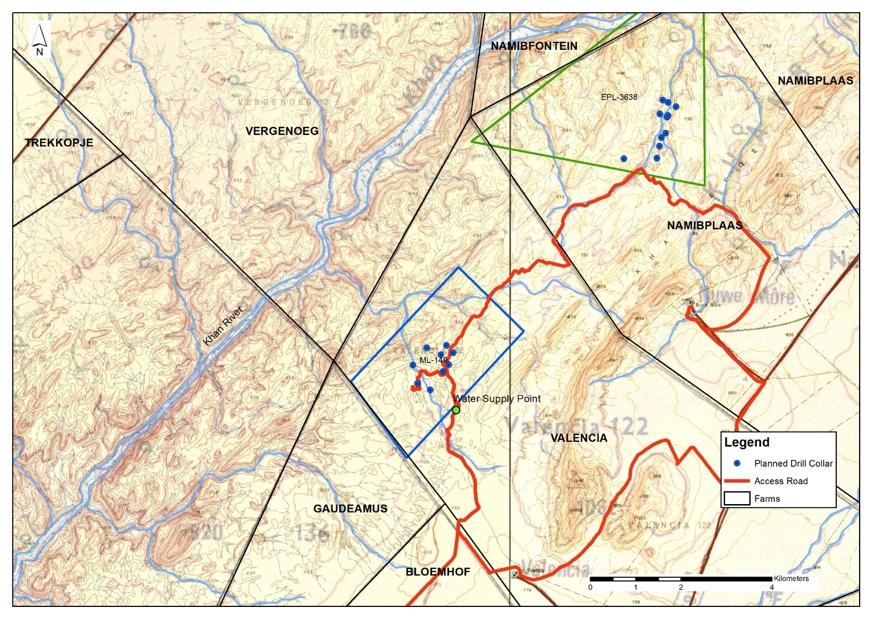
By the end of October 2023, a total of 1,445 m of RC drilling and 1,865 m of DC drilling had been completed, including substantial large diameter metallurgical drilling at the Valencia, ML-149 site. Work is ongoing and the majority of the programme is targeted for completion by year end 2023.
Further Resource Infill Drilling and Resource Extention Drilling
Planned Drilling targets in Valencia
- From historic ground radiometric survey data, areas of mineralization potential were delineated in view of resource upside and the proposed infrastructure development.
- Exploration targets / areas for sterilization drilling defined:
- Jolie Zone (~ 1km north of Valencia pit)
- Valencia West Extension
- Valencia South
- First campaign of 85 target percussion drill holes for 7,520 metres have been laid out on a 25 x 25 metre grid.
- objective is to more than double the quantity of the Measured Mineral Resource.
- holes target the 660 m elevation with drill depths up to 100 m from surface and is comparable to the previous Measured Resource grid.
A subsequent program for potential resource extension is planned for the areas adjacent to the Valencia Main deposit; along strike to the west, on the hinge zone to the south, and north of the Main deposit at the Jolie Zone.
Optimisation Work Plan
Pit Design Modeling
The updated resource block model is used to perform open pit economic models. Pit slope design parameters are being reviewed to include lithological logging and geo-mechanical test work from additional drilling. The preliminary pit designs are still subject to geotechnical confirmation testwork and 3-D fault modelling. The current pit designs are being used to optimize the mining fleet Capex and Opex for the different production scenarios and owner vs. contractor mining operation.
The project assumes a conventional open pit, drill, blast load and haul operations executed by a mining contractor. The mining Opex estimates were derived from mining schedules being developed within the design sequence of the various pits and pushbacks and mining cost proposals received from leading mining contractors. The primary alternative scenarios being considered are mill throughput at 7.5 Mtpa and 15 Mtpa respectively and Tank Leach vs. Heap Leach processing options.
The cut-off grade for each scenario also varies according to processing costs parameters and overall process recovery.
Column Leaching Process Optimization Work
Column Leach tests are presently underway at SGS in South Africa where the columns have been emptied and final analyses and data still to come. The next phase of testing is in planning and the work involves a systematic process to enhance the efficiency and effectiveness of extracting the uranium mineralisation from the ore using sulphuric acid solutions.
This comprehensive column leach program is designed to test a wider range of head grades, followed by composite samples selected according to the anticipated mining plan with respect to head grade and lithologies. In particular, the lower head grades to be tested with the concomitant reduction in resource head grade. This program is designed to test a range of leaching variables, including crushing by High Pressure Grinding Rolls (HPGR) to take advantage of the so-called particle cracking to expose increased mineral surface area for improved leaching. Column work to date has shown higher uranium grades in coarser fractions of the residue.
With lower cut-off grades, the head grades to be tested in this program range from 80ppm to 200ppm U3O8 in order to determine ore extraction potential. Variables to be tested include:
- Crushing methods (conventional vs HPGR) ahead of leach and crush size to be tested and traded-off.
- Curing time ahead of column
- Proportion of acid added to curing and agglomeration
- Acid dosage strength
- Acid irrigation rates
- Effect of binder.
- Mineralogical studies of feed and residues.
- Grading and size by analysis of feed and residues.
These envisaged tests involve evaluating the impact of HPGR generated particle size distribution on subsequent leaching processes and optimizing parameters to achieve desired leach outcomes.
Process Design
DRA Global were appointed as the study contractor to deliver high level engineering to provide preliminary cost estimate (PEA) for a heap leach process.
The methodology included mass balance and process block flow diagram to produce a preliminary sized mechanical equipment list (MEL). Pricing for major equipment items was sourced from the market. Factors deemed appropriate for the type of equipment were applied to compile the overall capital estimate. Layouts were prepared to determine conveyor lengths and earthworks quantities, in particular for the heap leach pads to refine cost estimates.
The MEL provided the basis for the power requirements and mass balance the basis for water requirements. Infrastructure supply costs were estimated based on the utility requirements and in turn provide utility tariffs for operating cost estimates.
Market pricing for reagents and consumables was sourced from the market for operating cost estimates. Labour costs benchmarked from other operating mines in the region.
Process Engineering Optimisation
The PEA process engineering design is being optimized in parallel with a focus on:
- Increasing confidence in equipment costing from the market by expanding specific Vendor equipment pricing.
- Value engineering of the flowsheet and optimizing layout and materials handling circuitry.
- Optimise heap leach cycle times to reduce residence time and reduce pad sizes.
- Optimise layout to reduce costly earthworks.
- Evaluate upfront Ore sorting to increase head grade to the process, discard waste and increase Run of Mine and metal quantities for processing.
- Critique acid supply, investigate bulk supply from the East and cost of delivery to site which is a major contributor to processing cost.
- Value engineer major operating cost contributors including hydrogen peroxide, power (optimize crushing and materials handling circuitry) and water (more detailed mass and water balancing).
Bulk Sampling
After site assessment and selection, a detailed plan is being drawn up to develop a box cut with the objective of retrieving approximately 20,000 tonnes of typical run-of-mine a fresh and representative sample material from the orebody. Bulk samples are required for the following planned workstreams:
Sorting test work to upgrade the Run of Mine ore prior to leaching
HPGR crushing test work to provide prepared sample for bulk testing
- Large scale column testwork to inform process design
Pilot heap leach facility for confirming process design
Mining Licences, Environmental Certificates and Permits
The Company currently holds a 25-year Mining Licence (ML-149) for its Valencia deposit, valid until 2033. In September 2022, the Company also made an application to the Ministry to convert EPL 3638 to a full 25-year Mining Licence (“ML”), and this submission is pending as ML 251. EPL 3638 remains in good standing while the Ministry processes the Company’s ML 251 submission.
Earlier in the year, Forsys renewed its Environmental Clearance Certificate (“ECC”) from the Ministry of Environment, Forestry and Tourism for a further three-year term., allowing the Company to advance its development plans for the Norasa project. The ECC renewal process evaluated the Company’s environmental management practices, including waste management, emissions controls, biodiversity protection, and community engagement, among other factors.